A self-described lean manufacturing professional, Thomson Joseph spent the early part of his career in the water and construction industries before starting at German textile machinery manufacturer Trützschler’s Indian operations in 2010. “Trützschler was not lean when I joined,” he tells The CEO Magazine.
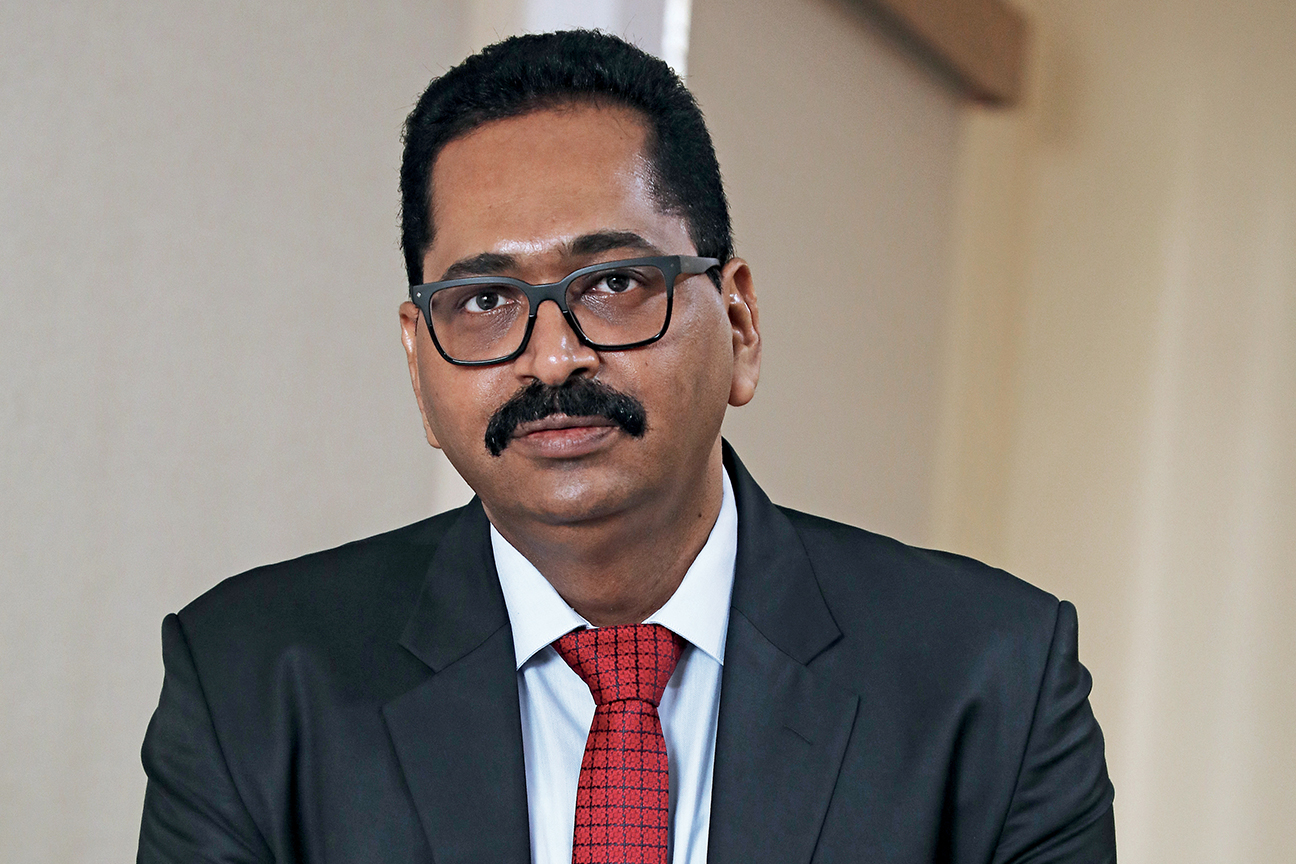
“I’ve introduced lean tools to the company.” In the decade since Thomson came on board as Senior Vice President, then as CEO in 2017, his ‘more with less’ philosophy has been the catalyst for its aggressive growth – even if, due to space constraints at its location in the city of Ahmedabad, the company hasn’t been able to expand its 41,737-square-metre plant physically.
“We’ve shrunk a lot of working spaces to make room for new products and new manufacturing areas,” Thomson explains. His team has been very supportive in joining him on this lean journey.
With the strong support of the parent company to the Indian subsidiary, additional product lines have been added as Trützschler India strives to become a major player in the textile machine manufacturing market, which includes domestic production of tuft blending machines for fibre blends and the modern high-production portal bale opener, BO-P.
“These are the products required for new generation spinning mills,” Thomson predicts. He is particularly enthusiastic about the potential that the local non-woven market holds. While the company is already a market leader in the segment internationally, on a local level the category is still “nascent”, according to the CEO.
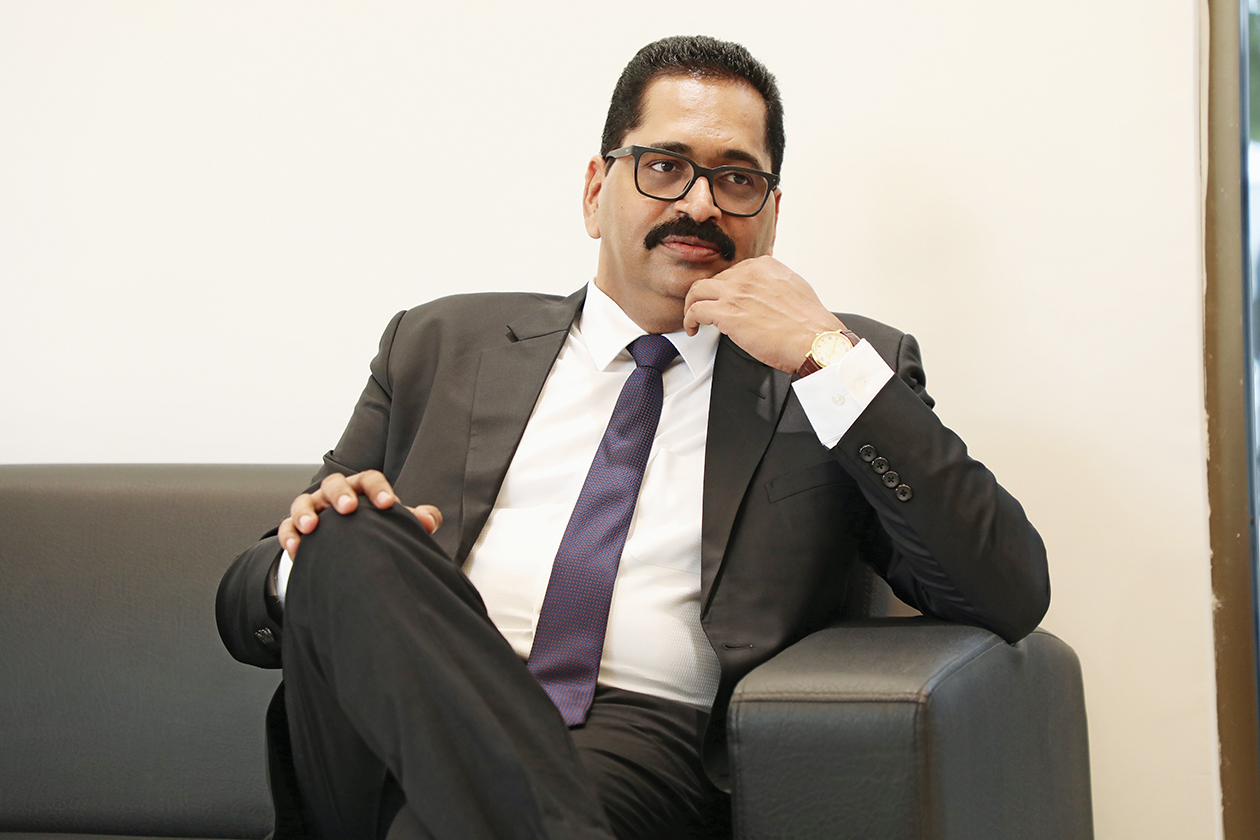
“For example, people around the world use tissues and wipes for personal hygiene applications,” he explains. “In India, we have yet to see large-scale usage of these disposable products.”
Yet, driven by a younger, tech-fluent generation and the growing demand for masks, aprons and other hygiene equipment in response to COVID-19, Thomson is predicting rapid change.
“Our presence in the non-woven segment in India is set to increase in a very big way,” he explains, adding that as long as there is a demand for its machines, Trützschler is ready to manufacture them locally.
Founded in Germany in 1888, the Trützschler brand has a global reputation for cutting-edge technology in the areas of spinning preparation, card clothing and non-wovens/BCF. It arrived in India in 1977, first under the name Trumac, and is a brand long synonymous with ‘made in Germany’ quality.
With factories in Germany, as well as the US, Brazil, China and India, the company is able to deliver the same equipment, no matter what the country of production is.
“Quality is inherent and a machine coming out of any of these manufacturing plants will be of identical quality,” Thomson says, adding that this is one of the key drivers of the business’s success, as are its intelligent products.
“We are known for innovation. We continuously strive to bring in the latest technology to not only improve ourselves but also bring value to our customers.” Earning market share with state-of-the-art machinery is one thing, but Thomson is well aware that retaining it is another matter. “It’s a key challenge for all of us,” he says.
Green machine
Thomson outlines some of the green initiatives Trützschler is undertaking locally: Fuel burners have been replaced by gas burners, rainwater is harvested before being filtered and used to water the ground, and the kitchen equipment in the canteen is solar powered (except for three months of the year during the rainy season). “In the past five years, we have also gone into woodless packaging and now only use wood for the bottom of crates. Over that time, we have saved 19,500 trees from being cut,” he explains.
“We always work on after-sales support because our job doesn’t end when we sell a machine.” Thanks to an increased network of engineers across India – who respond to call-outs in defined geographical zones from their home office base – offering clients a faster response time, the company has been able to improve its market presence on a countrywide scale.
As a lean expert leading a company and someone who continually seeks self-improvement, it’s little surprise that Thomson hasn’t missed a beat in identifying the business lessons of the pandemic.
“The manufacturing processes cannot be the same because of social distancing and the new hygiene standards that need to be implemented,” he says. “We have had to reorientate the whole manufacturing shop floor, educate our employees with new COVID-19 guidelines and regularly sanitise the production floor.”
Beyond the immediate changes, Thomson foresees a shift in HR strategy. “We may have to look for people from different geographical areas of the city or locality so that if one place is declared a hotspot and those who live there are forbidden to come to work, we can still keep the operations running because we have members of the team coming from outside that area,” he says.
He also believes that multiskilling will increase in importance as companies look to protect against similar lockdown scenarios in the future. “We are developing plans to expand our employees’ skill sets so that if something happens again other employees can step into another section,” he continues.
Another trend that the coronavirus has accelerated is automation. “Automation will allow us to have a high operating efficiency,” Thomson states. He stresses that the qualities found in every textile machine that rolls out of Trützschler’s global production line govern its culture and relations with employees, customers and suppliers. “Innovation, reliability, partnerships and quality are built into our culture,” he says.
Proudly supported by:
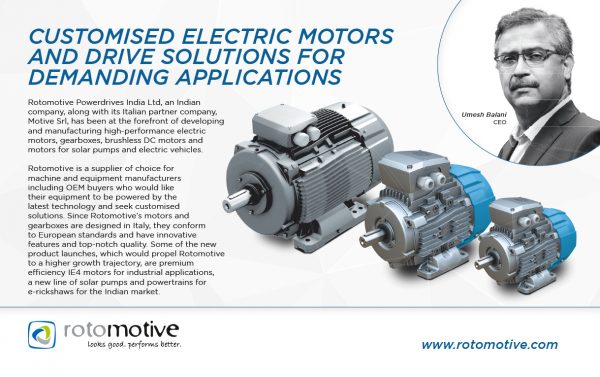